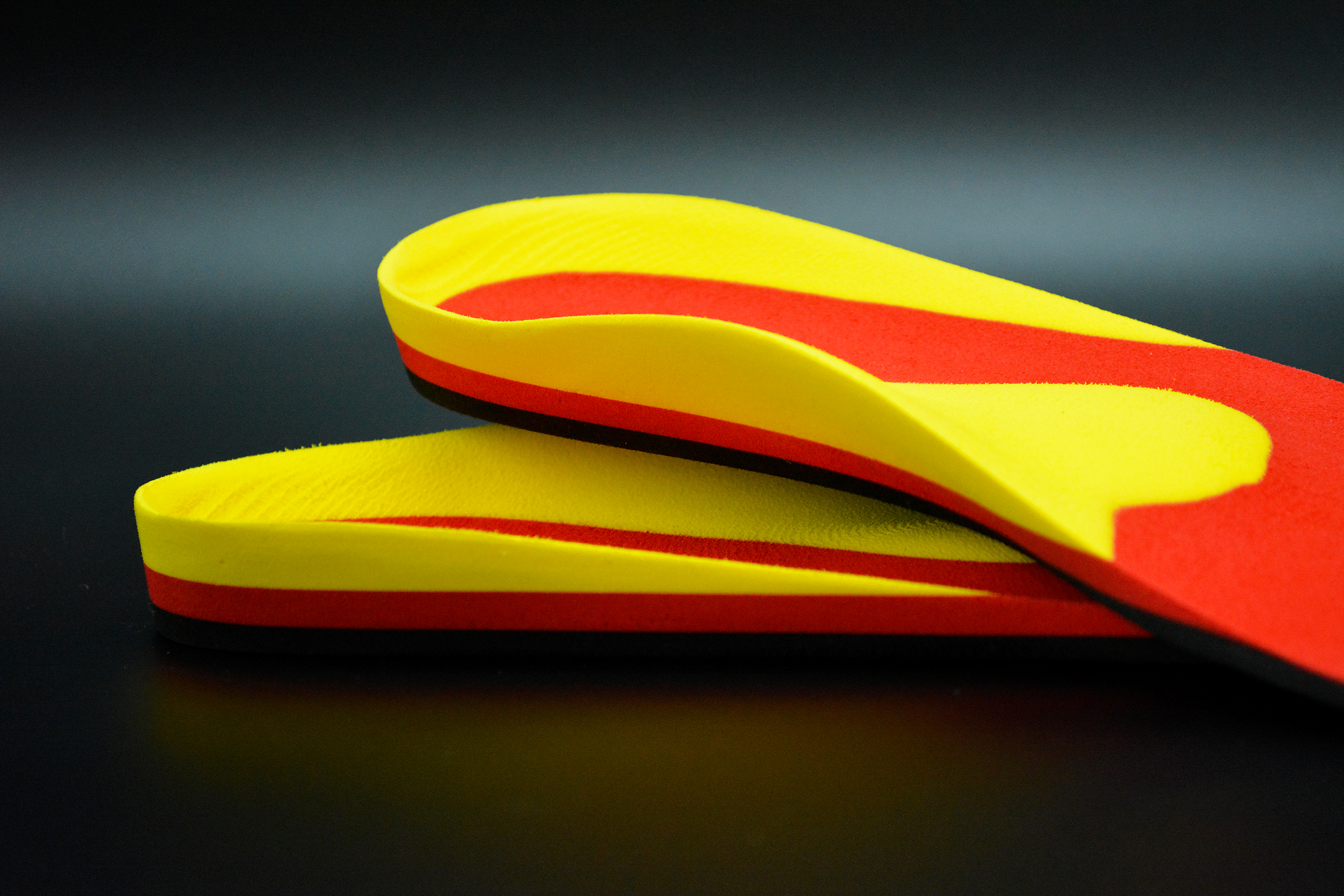
Dual-sided milled sports insole using Lunatec combi CAD 2
The perfect material for a dual-sided milled sports insoles: Lunatec combiCAD 2 is a vulcanised composite sheet made of 25 mm Lunatec CAD 35 (approx. 35 Shore A) and 7 mm Lunasoft Z (approx. 25 Shore A) as well as a 3 mm stabilising layer for optimal suction.
After examining and scanning the feet, the insoles are designed on a computer. The 3D-Scan does not replace the classical working steps like blue print or impression box. With the help of an online software the more detailed designing of the insoles and all important elements are being fit in hight and width exactly to the foot.
Then, this data is being transferred to the CAM-System. The Lunatec combiCAD2 milling block is cut to size and is firstly put into the milling machine with the bottom part to the top, and is milled on that side. Benefit: The insoles are customised exactly to the middle sole of the shoes that the patient is wearing.
The dual-sided milling saves valuable time of manual rework like extensive grinding.
The milling block is turned around and the individually designed shape of the insoles is being milled. Now, the insoles are milled out of the block, only the holding bar is remaining. The holding bars are cut with a knive and the insoles can be taken out of the block. Afterwards, the insoles become their finishing touches. Uneven parts can be removed with a polishing belt.
When working with the milling material a significant difference becomes apparent: The material is easy to work with and achieves excellent values when tested for elongation at break, tensile strengh and recovery time. Plus: There is no lamination, so there are no disruptive glue lines between layers.